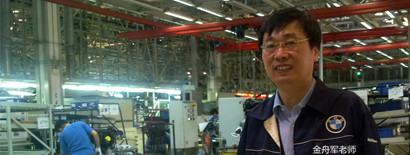
上海咨询公司精益生产管理培训公开课咨询课程—欢迎企业培训公开课和机构合作垂询
精益生产管理培训公开课-培训地点:江苏无锡万达广场 每月开班 小班教学、满四人开班
金舟军老师 手机/微信:13816949004 QQ邮箱:923503608@qq.com
以应用为导向的精益生产培训,学员培训后就会应用精益生产管理,金舟军老师通过严格的培训流程确保顾客满意
请点击查看—金舟军质量管理工具培训咨询实施流程
精益生产培训讲师质量专家金舟军,精益生产培训咨询机构上海科租企业管理咨询有限公司,是专业、实战的培训,精益生产培训,培训班和企业内训请垂询培训大纲,精益生产培训资料光盘赠送
最有价值的精益生产管理培训公司
上海科租企业管理咨询有限公司金舟军老师自办精益生产培训咨询公司,培训老师自办咨询公司省出了业务费用和老板利润,客户的培训费全部变为培训老师的培训费,能为客户提供优质服务,客户培训价值最大化值 。只要学员参加过质量培训课程,将为学员提供终生的培训课程答疑。
最具专业的精益生产培训讲师
金舟军二十多年专业从事精益生产培训讲师,专业涉及质量管理和精益生产课程,客户涉及世界五百强企业, 每个培训项目的客户都有培训现场的视频和照片为证。金舟军老师课程以应用为导向,课堂上只讲干货,绝不以无关的游戏打发时间。
培训客户-全部有客户培训现场照片、视频为证!


重庆长安汽车、上海延锋韦世通、上海NEC、上海德尔福、武汉东风汽车、江苏东风起亚、江苏麦格纳、安徽康佳电器、、安徽博西华、上海奥托立夫、浙江海信惠尔浦、沈阳宝马汽车、上海大金空调、辽宁大连固特异轮胎、长春大众集团、湖北武汉佛吉亚、上汽集团、吉林一汽集团、广西上汽通用五菱、广西玉林重工、江西长力股份 北京北汽福田、深圳中兴通迅、福建新能源科技、湖南三一重工、苏州恩斯克轴承、河北天威光伏、武汉哈金森、苏州力特奥维斯、重庆 嘉陵集团 福建奔驰汽车、辽宁大连大众变速箱 广东广州京信通信、深圳中兴通讯 河南利达光电 河南新乡豫新 河北莱尼、山东莱尼 、山东胜地、陕西中航、湖南时代电气、天津中核
精益生产管理培训课程公开课视频--点击图片即观看好看金舟军老师好看视频主页
金舟军老师精益生产培训优势精益生产管理培训课程公开课视频--点击图片即观看好看金舟军老师好看视频主页
结合客户案例的实战型培训 包括后服务答疑的全过程
金舟军老师通过五大步骤结合客户案例讲解,确保学员学完全就会在工作中应用: 1 .案例网络调研、2.案例学员预习、3. 现场案例调研、4.案例练习点评、5.售后案例答疑。
1.案例网络调研
培训意向一经确定,金舟军老师就要与客户进行网络沟通,确定精益生产实施难点,收集精益生产实施资料,并就实施资料的细节进行沟通,并了解客户学习精益生产的目的。
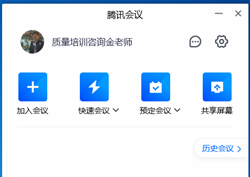
2.学员案例预习
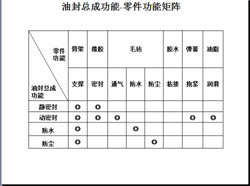
3. 现场案例调研
金舟军老师根据精益生产实施中的难点,事先为学员出精益生产的预习题,帮助学员提前思考怎样解决实施案例的难点,同时也预习课堂讲解的知识。
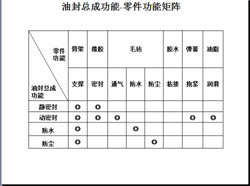
3. 现场案例调研
培训前一天,金舟军老师会到客户现场进行一天的现场调研,查找客户精益生产实施V情况,并为课堂针对客户实施精益生产中的问题讲解做准备。
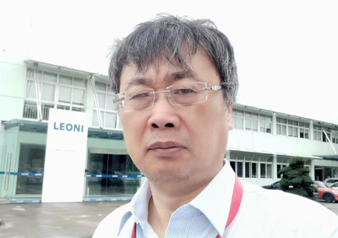
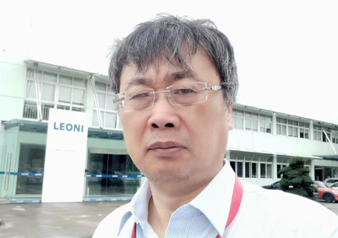
4.案例练习点评
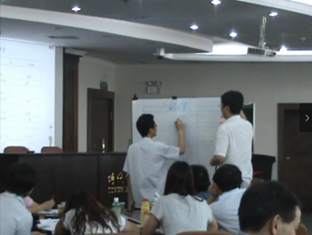
5.售后案例答疑
培训完成后一年之内,如果客户在实施精益生产过程中有什么问题,可以为客户组织腾讯会议的在线答疑至少三次。
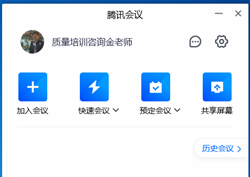
根据案例实施中的难点问题,每天培训约有五十分钟的客户案例分组练习,每组学员的案例练习金舟军老师都要做详细的点评,确保学员学完全就会在工作中应用。
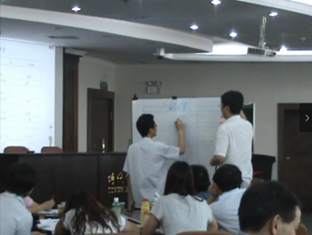
5.售后案例答疑
培训完成后一年之内,如果客户在实施精益生产过程中有什么问题,可以为客户组织腾讯会议的在线答疑至少三次。
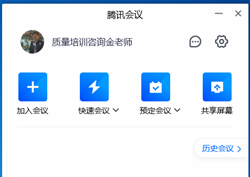
< 精益生产管理培训课程公开课现场照片
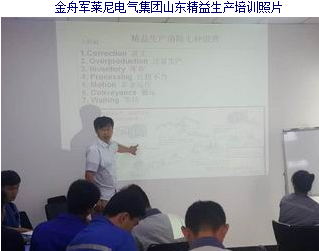
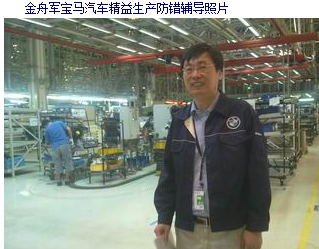
精益生产管理培训
课程公开课大纲
一.培训目的:通过学习,学员能掌握精益生产的方法,并能利用拉动式准时化生产、目视管理、看板管理、
价值流分析、流线生产线布置等方法消除企业中的七种浪费。
二.培训对象:生产管理、质量管理、现场管理人员和班组长。
三.课程内容
1.精益生产产生背景 金舟军原创抄袭必告
生产的本质
两种生产方式
TPS丰田生产方式
福特大规模少品种生产方式
案例讨论-两种生产方式各自的金优缺点
2.精益生产原理
精益生产系统
实施精益生产的基础
案例讨论-实施精益生产的基础有哪些
3.精益思想的五个基本原则
价值原则VALUE
价值流原则VALUESTREAM
流动原则FLOW
拉动原则PULL
尽善尽美原则PERFECTION
案例讨论-尽善尽美原则包括哪些内容
4.精益生产消除七种浪费
浪费的定义MUDA
过量生产浪费
库存浪费
搬运浪费
返工浪费
过程不当浪费
多余动作浪费
等待浪费
案例讨论-过量生产浪费产生的原因有哪些
5.柔性生产
通过时间
进料仓库到出货仓库时间(DTD)
制造周期时间(MCT)
案例讨论-怎样减小制造舟周期时间
6.价值流分析 金舟军原创抄袭必告
精益生产创造价值的原则
生产增值比率
过程价值流分析方法
创造价值的过程
公开的浪费的过程
隐蔽的浪费的过程
价值流程图ValueStreamMapping
案例讨论-客户某一生产过程价值流分析
7.过程风险分析
过程风险严重度
过程风险发生率
过程风险评价
过程风险的预防措施
案例讨论-客户某一生产过程风险的舟预防措施
8.作业切换时间
内部切换时间
外部切换时间
快速换模SMED
作业切换时间减小的方法
案例讨论-客户某一生产过程外部切换时间减少
9.单件流 金舟军原创抄袭必告
无停顿和堵塞的生产流程
机器别布置
工艺顺布置CELL
单元U型平面布局图
案例讨论-客户某一生产过程U型平面布局图
10.节拍生产
用户节拍是工厂的脉搏
循环时间Cycletime与节拍时间Takttime
基于节拍时间优化循环时间
案例讨论-怎样实现某产品生产各工序循环时间与节拍时间一致
11.拉动生产
只有当用户订货时才生产
精益生产过程自动调整
推动与拉动
生产信息和物料的流动
看板Kanban管理
看板运行流程
看板主要内容
看板数量计算
案例讨论-客户某一生产过程看板数量计算
12.零缺陷 金舟军原创抄袭必告
过程质量决定产品质量
两种零缺陷及其实现方法
停产分析解决问题
5Why找出根本因
首次通过率
案例讨论-客户某一生产过程实现零缺陷的方法
13.自働化
防错=自働化
自働化两大功能
三种检验方法
判断检验
信息检验
溯源检验
案例讨论-客户某一生产过程溯源检验实现零缺陷的方法
14.防错
十种人为错误
人员三个方面的错误
防错两种功能
三种类型防错方法
触碰式防错法
固定数值防错法
动作步骤探测防错法
案例讨论-客户某一生产过程溯源检验实现零缺陷的方法
15.TPM全面设备维护
设备管理七大损失
OEE设备综合效率
时间开动率
性能开动率 金舟军原创抄袭必告
合格品率
自主维护AutonomousMaintenance
自主维护三个活动
自主点检检查表项目
日常点检表范例
设备清扫清单
预测性维护
预防性维护
计划维护
案例讨论-设计一个自主点检军检查表
16.透明工厂
可以认清与额定值的偏差
目视管理
颜色管理
生产目视化管理
目视化每日/周/月维护
目视化质量状况
目视化产品检验状态
定置管理图
案例讨论-螺丝拧紧颜色管理
17.持续改进CIP
持续改进Kaizen
系统改进步骤
纠正措施vs纠正
确定根本原因三步法
—直到达到卓越的过程。
案例讨论-三步法分析根本原因
18.标准化作业
标准作业指导书
标准作业的生产节拍
标准作业步骤或要素
标准在制品量 金舟军原创抄袭必告
每项改进的基础
案例讨论-三步法分析根本原因
19.现场负责
出现在距创造价值近的地方
经理现场负责
工厂指标在现场
员工参与编制作业指导书
案例讨论-为什么要员工参与编制作业指导书
20.零浪费
减少浪费是持久的挑战.
识别浪费的方法
减少浪费的方法
案例讨论-实现零浪费的措施有哪些.
21.5S实施精益生产的基础
整理整顿清扫清洁素养
必需品和非必需品的基准表
清扫清单
案例讨论-5个S之间是什么关系
22.定置管理
工艺研究确定物流布置
人机工程确定工位布置
案例讨论-工位布置置要考虑哪些因素
四.课程学时:每天6.5小时共2-8天
精益生产培训
宝马汽车VPS课程大纲
本课程为精益生产的实战课程,培训师金舟军作为宝马汽车精益生产VPS讲师参与开发中国宝马中国精益
生产VPS培训课程,并为中国宝马开展过十几天的各阶层精益生产VPS培训,本培训教材即是宝马中文精益生产VPS
教材。具有实战简洁之特点,使学员掌握五百强企业精益生产之精华。
一.培训目的:通过学习,学员能掌握精益生产的方法,并能利用过拉动式准时化生产、目视管理、看板管理、价
值流分析、流线生产线布置方法消除七种浪费。。
二.培训对象:产品设计开发人员、售前售后工程师、过程设计核心成员。
三.课程内容
精益生产产生背景
精益思想的五个基本原则
实施精益生产的基础
精益生产消除七种浪费
精益生产创造价值的原则
创造价值的定向原则
常见的七大浪费
过量生产浪费
库存浪费
搬运浪费
返工浪费
过程不当浪费
多余动作浪费
等待浪费
价值流分析
10项精益生产过程原则
灵活性
-精益生产的核心强势
单件流
-无停顿和堵塞的生产流程
节拍
—用户节拍是工厂的脉搏
拉动
-只有当用户订货时才生产
零缺陷
—过程质量决定产品质量
透明工厂
—可以认清与额定值的偏差
持续改进CIP
—直到达到卓越的过程。
标准化作业
-每项改进的基础。
现场负责
-出现在距创造价值近的地方
零浪费
-减少浪费是持久的挑战.
5S实施精益生产的基础
四.课程学时:每天七小时共2天
精益生产培训机构上海科租企业管理咨询有限公司
精益生产及其产生
精益生产,又称精良生产,其中“精”表示精良、精确、精美;“益”表示利益、效益等等。精益生产就是及时制造,消灭故障,消除一切浪费,向零缺陷、零库存进军。它是美国麻省理工学院在一项名为“国际汽车计划”的研究项目中提出来的。它们在做了大量的调查和对比后,认为日本丰田汽车公司的生产方式是最适用于现代制造企业的一种生产组织管理方式,称之为精益生产,以针对美国大量生产方式过干臃肿的弊病。精益生产综合了大量生产与单件生产方式的优点,力求在大量生产中实现多品种和高质量产品的低成本生产。
一、精益生产的产生与推广
20世纪初,从美国福特汽车公司创立第一条汽车生产流水线以来,大规模的生产流水线一直是现代工业生产的主要特征。大规模生产方式是以标准化、大批量生产来降低生产成本,提高生产效率的。这种方式适应了美国当时的国情,汽车生产流水线的产生,一举把汽车从少数富翁的奢侈品变成了大众化的交通工具,美国汽车工业也由此迅速成长为美国的一大支往产业,并带动和促进了包括钢铁、玻璃、橡胶、机电以至交通服务业等在内的一大批产业的发展。大规模流水生产在生产技术以及生产管理史上具有极为重要的意义。但是第二次世界大依以后,社会进入了一个市场需求向多样化发展的新阶
段,相应地要求工业生产向多品种、小批量的方向发展,单品种、大批量的流水生产方式的弱点就日渐明显了。为了顺应这样的时代要求,由日本丰田汽车公司首创的精益生产,作为多品种、小批量混合生产条件下的高质量、低消耗进行生产的方式在实践中摸索、创造出来了。
1950年,日本的丰田英二考察了美国底持律的福特公司的轿车厂。当时这个厂每天能生产7000辆轿车,比日本丰田公司一年的产量还要多。但丰田在他的考察报告中却写道:“那里的生产体制还有改进的可能”。
战后的日本经济萧条,缺少资金和外汇。怎样建立日本的汽车工业?照搬美国的大量生产方式,还是按照日本的国情,另谋出路,丰田选择了后者。日本的社会文化背景与美国是大不相同的,日本的家族观念、服从纪律和团队精神是美国人所没有的,日本没有美国那么多的外籍工人,也没有美国的生活方式所形成的自由散漫和个人主义的泛滥。日本的经济和技术基础也与美国相距甚远。日本当时没有可能全面引进美国成套设备来生产汽车,而且日本当时所期望的生产量仅为美国的几十分之一。“规模经济”法则在这里面临着考验。改进改进对于每个人都是理所当然,每个人都要愉快地为改进出一份力,改进是我们日常工作的出发点。小改进将立即实施。每个过程都能够作改进并且每项改进都注入某个标准中。每个标准又是继续改进的出发点。
Kaizen
Kaizen意味着改进,涉及每一个人、每一环节的连续不断的改进:从最高的管理部门、管理人员到工人。持续改善的策略是是日本人竞争成功的关键
纠正措施vs纠正
为一劳永逸永久地解决问题,使问题不再发生,要针对问题的根本原因采取纠正措施,而非仅针对问题本身采取
纠正。
纠正措施correctiveaction
为消除已发现的不合格或其他不期望情况的原因所采取的措施
纠正correction
为消除已发现的不合格所采取的措施。
标准
标准通常是最聪明的解决办法。使经验交流变得容易一些,每个过程都遵循某个标准。我们的创造力将不断地提高这些标准。
标准作业指导书
标准作业是指把生产过程中的各种要素(人、机、料、法、环、测)进行最佳组合,按生产要求制定出相适应的作业标准。作业人员按照作业标准进行操作。
现场负责
经理在现场办公,定期与工人对话,直接就在发生问题的地方解决问题。
三现主义指的是现场、现物、现实,当发生问题的时候,管理者要快速去“现场”,观察“现物”,探究“现实”,找出问题原因和落实解决办法。