BIQS培训公开课-培训地点:江苏无锡万达广场 每月开班 小班教学、满四人开班
金舟军老师 手机/微信:13816949004 QQ邮箱:923503608@qq.com
以应用为导向的GM通用BIQS培训咨询,学员培训后就会应用通用BIQS,金舟军老师通过严格的培训流程确保顾客满意。
金舟军老师 手机/微信:13816949004 QQ邮箱:923503608@qq.com
以应用为导向的GM通用BIQS培训咨询,学员培训后就会应用通用BIQS,金舟军老师通过严格的培训流程确保顾客满意。
请点击查看—金舟军质量管理工具培训咨询实施流程
最有价值的通用BIQS培训咨询公司
金舟军老师BIQS培训优势最有价值的通用BIQS培训咨询公司
上海科租企业管理咨询有限公司金舟军老师自办通用BIQS培训lpa分层审核培训公司,培训老师自办公司省出了业务费用和老板利润,客户的培训费全部变为培训老师的培训费,能为客户提供优质服务,客户培训价值最大化值 。只要学员参加过质量培训咨询课程,将为学员提供终生的培训课程答疑。
最具专业的GM通用BIQS培训讲师
金舟军二十多年专业从事通用BIQS培训咨询讲师,专业涉及质量管理和精益生产课程,客户涉及世界五百强企业, 每个培训项目的客户都有培训现场的视频和照片为证。金舟军老师课程以应用为导向,课堂上只讲干货,绝不以无关的游戏打发时间。
通用BIQS管理培训的客户-全部有客户培训现场照片、视频为证!
通用BIQS管理培训的客户-全部有客户培训现场照片、视频为证!

重庆长安汽车、上海延锋韦世通、上海NEC、上海德尔福、武汉东风汽车、江苏东风起亚、江苏麦格纳、安徽康佳电器、、安徽博西华、上海奥托立夫、浙江海信惠尔浦、沈阳宝马汽车、上海大金空调、辽宁大连固特异轮胎、长春大众集团、湖北武汉佛吉亚、上汽集团、吉林一汽集团、广西上汽通用五菱、广西玉林重工、江西长力股份 北京北汽福田、深圳中兴通迅、福建新能源科技、湖南三一重工、苏州恩斯克轴承、河北天威光伏、武汉哈金森、苏州力特奥维斯、重庆 嘉陵集团 福建奔驰汽车、辽宁大连大众变速箱 广东广州京信通信、深圳中兴通讯 河南利达光电 河南新乡豫新 河北莱尼、山东莱尼 、山东胜地、陕西中航、湖南时代电气、天津中核
培训公开课和企业内训现场视频--点击图片即观看好看视频或金舟军老师好看视频主页
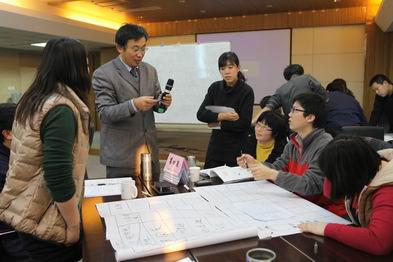
GM通用BIQS培训咨询
培训的周期一般是天-10天,讲得细时间就长。咨询是15天到40天,具体体天数要根据目前企业运行BIQS的实际情况来决定,如果企业完全满足BIQS标准,咨询仅就GM通用BIQS和BIQS的差异进行,时间就比较短。
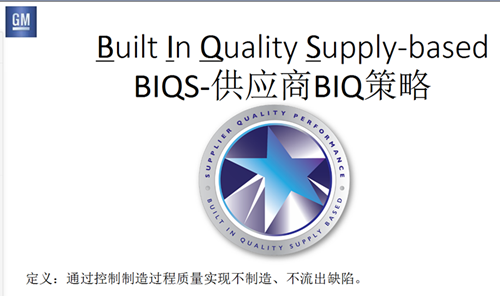
培训公开课和企业内训现场视频--点击图片即观看好看视频或金舟军老师好看视频主页
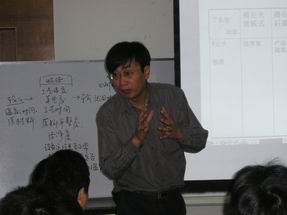
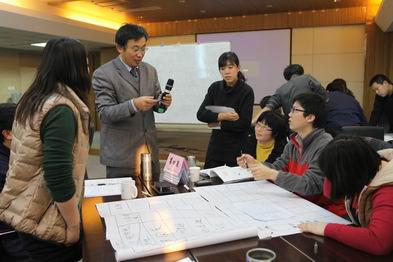
GM通用BIQS培训咨询
培训的周期一般是天-10天,讲得细时间就长。咨询是15天到40天,具体体天数要根据目前企业运行BIQS的实际情况来决定,如果企业完全满足BIQS标准,咨询仅就GM通用BIQS和BIQS的差异进行,时间就比较短。
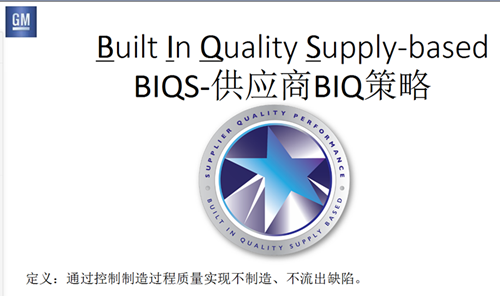
结合客户案例的实战型培训 包括后服务答疑的全过程
金舟军老师通过五大步骤结合客户案例讲解,确保学员学完全就会在工作中应用: 1 .案例网络调研、2.案例学员预习、3. 现场案例调研、4.案例练习点评、5.售后案例答疑。
1.案例网络调研
培训意向一经确定,金舟军老师就要与客户进行网络沟通,确定BIQS实施难点,收集BIQS实施资料,并就实施资料的细节进行沟通,并了解客户学习BIQS的目的。
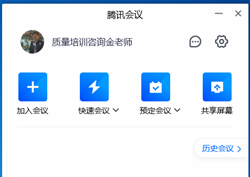
2.学员案例预习
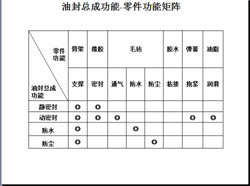
3. 现场案例调研
金舟军老师根据BIQS实施中的难点,事先为学员出BIQS的预习题,帮助学员提前思考怎样解决实施案例的难点,同时也预习课堂讲解的知识。
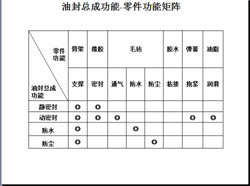
3. 现场案例调研
培训前一天,金舟军老师会到客户现场进行一天的现场调研,查找客户BIQS实施V情况,并为课堂针对客户实施BIQS中的问题讲解做准备。
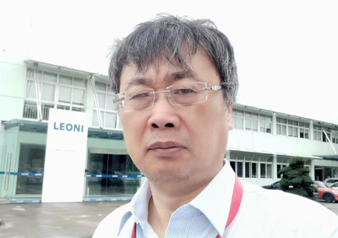
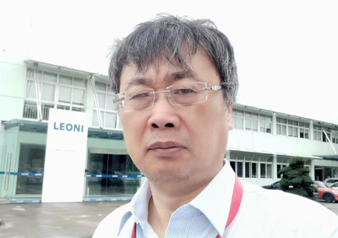
4.案例练习点评
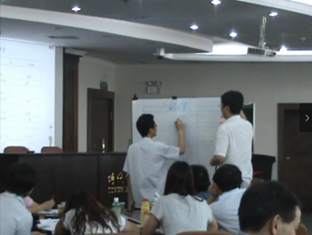
5.售后案例答疑
培训完成后一年之内,如果客户在实施BIQS过程中有什么问题,可以为客户组织腾讯会议的在线答疑至少三次。
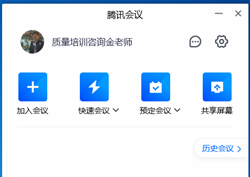
根据案例实施中的难点问题,每天培训约有五十分钟的客户案例分组练习,每组学员的案例练习金舟军老师都要做详细的点评,确保学员学完全就会在工作中应用。
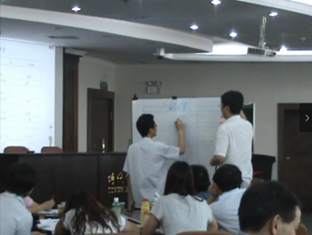
5.售后案例答疑
培训完成后一年之内,如果客户在实施BIQS过程中有什么问题,可以为客户组织腾讯会议的在线答疑至少三次。
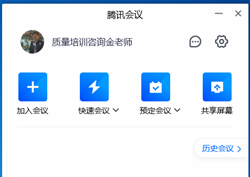
GM通用BIQS
BIQS的全称是Built-InQualitySupply-based,通用汽车在内部工厂使用的质量体系为BIQ,应用到供应商那边就称为BIQS。通用汽车将质量体系和方法分享给供应商。BIQS是QSB+(QualitySystemsBasic+)的升级版本。从BIQS通过提升制造过程质量,减少检查和纠正的投入,降低整体通用BIQS。
BIQS的全称是Built-InQualitySupply-based,通用汽车在内部工厂使用的质量体系为BIQ,应用到供应商那边就称为BIQS。通用汽车将质量体系和方法分享给供应商。BIQS是QSB+(QualitySystemsBasic+)的升级版本。从BIQS通过提升制造过程质量,减少检查和纠正的投入,降低整体通用BIQS。
通用汽车GMBIQS的30个模块
1 Nonconforming Material/Material Identification 不合格材料与材料标识
2 Layered Process Audit 过程分层审核
3 PFMEAs 过程潜在失效模式及后果分析
4 PFMEAs-Risk Reduction&Annual ReviewPFMEA-风险降低与年度评审
5 By Pass Management 应急替代管理
6 errorproofing Verification 防错装置验证
7 Gage Calibration/Measurement SystemAnalysis 量检具校准+测量系统分析
8 Fast Response Problem Solving Process 快速反应问题解决流程
9 TeamProblem Solving Process 团队问题解决流程
10 Quality Focused Checks 质量关注检查
11 Standardized Work 标准化作业
12 Process Change Control 过程变更控制
13 Verification Station(FinalInspection/CARE/GP12) 验证岗位(最终检测/CARE/GP12)
14 Change Control-Production Trial Run(PTR) 变更控制-量产试运行/PTR
15 Andon System Implementation 按灯系统实现
16 Alarmand Escalation 报警及逐级上报
17 Visual Controls 目视化控制
18 Visual Standards-Communicatedand Understood 目视化标准-沟通与理解
19 Process Control 过程控制
20 Process Control Plan Implemented 过程控制计划实施
21Process Capability Review 过程能力评审
22 Rework/Repair Confirmation 返工/返修确认
23 Feedback/Feedforward 后馈与前馈
24 Training 培训
25 Contamination Requirements 异物要求
26 Maintenance 维护
27 FIFO/Material Handling Process先进先出与材料处理流程
28 Shipping Approved Packaging 批准包装发运
29 SupplyChainManagement 供应链管理
30 Safety 安全
25 Contamination Requirements 异物/清洁度管理要求
产品(零部件,半成品,成品)有防护,以免异物和灰尘进入。
审核关注点:
1 .确认产品或生产环境是否有清洁度要求,比如无尘车间,发动机的清洁度要求等.
2.查看清洁度检查的标准作业要求(如作业指导书、使用的工具或设备、检查频次)和记录,验证供应商按要求检测,进行趋势监控并对超差或者失控的点有行动措施。
3.在线检查产品/原材料的防护和储存方法,是否能避免异物或零件损坏.
26 Maintenance 设备维护管理要求:
1.工艺、制造和设备维护共同努力通过TPM实现生产的持续良好运转
2.对 备件需求和存储有管理
3. 关键部件需要识别出来
4.维护保养计划需要包含设备和工装,制定预防性/预见性维护计划
审核关注点:
1.检查供应商的维护保养计划和记录,确认按计划实施。
2. 检查维护保养团队的标准化作业,人员技能及培训记录。
3. 检查设备MTTR和MTBF数据,如果目标没有完成,询问行动计划。
4.检查备品备件库,检查最大/最小库存要求和跟踪实际库存,存储环境要求,先进先出,寿命要求等。抽检备件验证是否能很快被找到。
27 FIFO/ Material Handling Process 先进先出/物料搬运过程要求:
1.在所有工位都需要有材料先进先出的要求和管理,用目视化来辅助实现先进先出
2.在制品包装,料架,料框能够保护零件不被损坏
审核关注点:
1.查看供应商先进先出流程要求,流程需要包含靠墙的零件、按列摆放零件、货架上零件的FIFO管理。
2.物料根据生产日期或生产批次来进行FIFO摆放.
3.检查不同区域的先进先出,特别是有有效期的原材料,检查是否有目视化来帮助实现先进先出。
4.查看仓库和生产现场,确认零件的摆放和搬运过程不会对零件产生损坏。
28 Shipping Approved Packaging 认可的发货包装要求:
1.所有可销售的批量生产产品都需要有正确的标签和批量生产包装
2.在制品的包装箱或容器能够保护产品
审核关注点:
1.查看产品的出货包装及包装批准记录(如GM1738i),检查实际的包装和贴标签过程,以确认零件得到保护,同时确认供应商如何做到包装和标签的防错。
2.对在制品,查看料框、料架,确认零件的防护。
29 Supply Management 供应商管理要求:
二级供应商管理的目标需要被定义并且要跟踪供应商的表现.
审核关注点:
1.检查供应商管理流程及记录,流程需要包括:潜在供应商评审,APQP要求,量产质量管理(如质量表现跟踪,问题解决,变更管理,年度审核等要求)。
2.检查供应商审核计划和执行程度,询问是否有高风险供应商的管控,查看审核表是否包含了BIQS1-13的最低要求。
3.回顾供应商的问题解决报告,验证供应商有有效的问题解决流程。
30 Safety 安全
领导层负责公司健康安全要求的实施和监督,以建立完善的员工健康及安全文化。
--目前 30不算分,对于现场发现的安全问题,会在总结会上提出来。